整体式环模。整体式环模的主要结构参数有:环模直径、环模厚度、环模有效宽度、模孔形状、模孔直径、模孔有效深度、模孔间壁厚以及环模的压缩比、粗箍度等。
环模模孔的长度与模孔直径的比值习惯上称为环模的压缩比它是反映燃料颗粒挤压强度的一个重要指标。压缩比越大,挤出的燃料密度越大,对于成型秸秆类生物质压缩比一般为6~10左右。
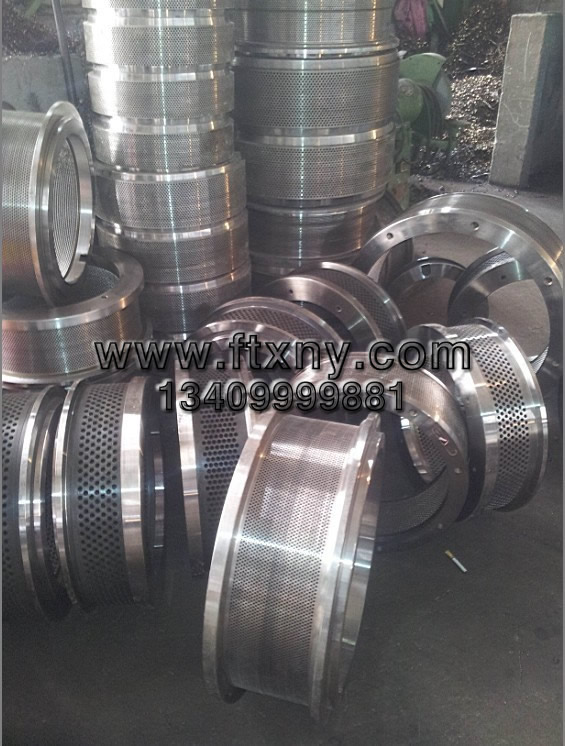
环模模孔开孔率越高,则出料越多,有利于提高生产率,但模孔间壁厚度变小,环模强度减小,容易开裂,所以要选择合适的壁厚来保证环模的强度和开孔率。一般来说,模孔直径越大,环模的开孔率越高;开孔率越高,出料越通畅,但环模强度也降低了。成型挤压力大的原料,环模的开孔率适当小一些,保证环模的强度,防止环模开裂。
环模的厚度直接影响产品质量,环模的工作面积与设计功率成正比,功率一定对,环模应有对应的有效宽度,一般环模的有效宽度为10~14cm,分体模块式环模大一些,颗粒环模小一些。环模厚度是一个关键参数,其影响因素很多,要根据不同原料种类经过认真工程试验再定型。环模成型腔和压辊是环模成型颗粒机的核心部件,其中的成型腔设计和加工又是关键技术,因此要对设备应用的范围、对象等作详细分析,不可一概而论,不可能有万能成型颗粒机,要做多因素分析。
整体式环模磨损后需要整体更换,不仅增加维修成本,还会严重影响企业正常生产。因此环模材料的选用显得尤为重要。目前,我国整体式颗粒环模成型颗粒机多数是沿用颗粒饲料成型颗粒机的设计,选用4Cr13不锈钢和42CrM04合金结构钢作为环模的材料。4Cr13不锈钢的刚度和韧性都较好,采用整体淬火热处理后,其硬度大于HRC50,并具有良好的耐磨性和耐腐蚀性,使用寿命较长。42CrM04合金结构钢的机械强度高,淬透性高,韧性好,淬火时变形小,高温时有较高的蠕变强度和持久强度。
用秸秆类原料生产颗粒成型颗粒燃料是不合算的,粉碎能耗高,磨损快。秸秆原料含有较高的碱性氧化物,成型孔磨损很快,在硬度小于HRC60的条件下,维修周期在300 h左右,可扩孔维修1或2次,但成型率降低。二次维修周期更短,因此秸秆颗粒是不适宜用整体环模技术的。
套筒式环模。套筒式环模由母环和套筒组成,套筒安装在母环上。套筒的模孔可按成型理论单独设计加工。模孔的结构应具有预压成型段、成型段和保型段,各段尺寸应设计合理。套筒与环模可通过螺纹或嵌入的方式套装。由于采用了套筒模孔,套筒模孔磨损后可实现快速更换,从降低设备加工成本和节约维修成本方面分析,套筒式环模优于分体模块式环模。
套筒式环模要注重三个方面技术的应用,一是母环的设计与加工,原则上母环的整体是不更换的,因此它的强度和成型套筒座的尺寸精度要保证,为降低成本可用铸造技术生产。二是套筒的设计,内孔要有保证燃料质量的成型角和保型段长度,外部尺寸要满足母环要求。材料可以是非金属材料,也可以是耐磨铸铁材料。三是要更换方便,便于用户操作。
套筒环(平)模在成型颗粒燃料发展中具有方向性,需要重点解决的是盘面的磨损维修与套筒更换的一致性。
分体模块式环模。分体模块是环模的核心部件。模块入口部位的结构是生物质压缩成型的关键技术之一,其结构尺寸、加工质量和精度直接影响环模的使用寿命,以及成型颗粒机生产能力和产品质量,对用户的使用成本也有很大影响。根据生物质成型理论可将模块组合后的成型腔分为三个阶段:预压阶段、成型阶段和保型阶段。
成型腔中的生物质原料进入模辊间隙到压缩终了称为预压阶段,分体模块模孔的人孔坡口,模辊间隙、料层厚度、压辊转速等参数影响预压效果。模辊间隙大、料层厚、压辊转速高,预压效果变差,磨损加快、耗能增加。从模孔坡口下端到保型段开始为成型阶段,模孔这一部分的结构应设计成内锥形,成型角一般为10~30。这一段是保证原料产生塑性变形所需的挤压力和成型密度的关键阶段,原料对模孔的磨损最为严重,对模块热处理性能特别是耐磨性要求较高,成型角磨损变化后,成型率就会降低,分体模块就要更换。实践证明,更换是成批的,不可能是个别的;成型段过后,密实原料进入保型段,这一段的直径略大于成型段出口尺寸,作用是消除在成型段产生的内应力,使成型颗粒燃料达到松弛密度的工艺要求,成为最后产品。
由上述分析可以看出,分体模块的模孔具有成型和保型的功能,模孔的长度即分体模块的厚度也应保证成型和保型功能的实现。成型和保型段的长度应根据不同种类原料的特性、模孔形状、成型块截面面积及要求的成型密度来确定。目前市场上的分体模块式成型颗粒机大都将模块厚度设计得比较小,保型段的长度不够长,使得成型效果不好、成型质量不高。加工30~50 mm的棒(块)状成型颗粒燃料,分体模块模孔的长度不得小于10cm,与燃料断面尺寸的比一般为1:(6~8),可根据不同条件变化。
模块失效的形式主要表现在两个方面:一是模孔人口处产生的严重磨损和应力集中导致开裂而报废,如图6.7所示;二是保型段过度磨损而报废。模块的使用寿命不仅仅与选用的材料、加工工艺有关,还与生物质原料类型、燃料成型工艺参数、操作方法有密切关系,即使相同的模块材料和相同的加工工艺,当上述条件不同时,模块的使用寿命也相差很大,尤其县檬孔人口处的磨损和开裂更为突出。
分体模块的材料可根据成型的生物质原料种类、物理特性来选用。一般加工棒状或块状成型颗粒燃料可选用35号或45号优质碳素结构钢,以及20Cr、40Cr、40CrMnMo等合金结构钢,重要的是上述材料的热处理工艺和磨损后的修补方法。
由于分体模块式环模磨损后是群体换修,因此工作量和成本都比较高,其难度不比整体式维修小,对燃料生产单位来说,操作难度高,这是工程化阶段出现的新问题。因此要进行技术集成再创新,目前本书参编单位采用的金属喷涂工艺取得较好效果,但受条件限制也不能到设备使用单位进行维修。
(转载请注明:意甲直播cctv5颗粒机)